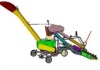 | Агроинженерные системы |
| 1 | 2 | 3 | 4 | 5 |
|
|
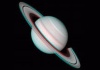 | Астрономия |
| 1 | 2 | 3 |
|
|
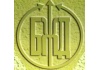 | Безопасность |
| 1 | 2 | 3 |
|
|
|
|
|
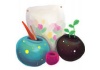 | Искусствоведение |
| 1 | 2 | 3 | 4 | 5 |
|
|
|
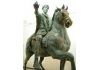 | Культурология |
| 1 | 2 | 3 | 4 | 5 | 6 | 7 | 8 |
|
|
|
|
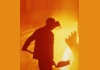 | Металлургия |
| 1 | 2 | 3 | 4 | 5 |
|
|
|
|
|
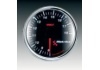 | Приборостроение |
| 1 | 2 | 3 | 4 | 5 | 6 | 7 | 8 | 9 |
|
|
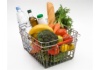 | Продовольственные продукты |
| 1 | 2 | 3 | 4 | 5 | 6 |
|
|
|
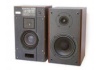 | Радиотехника |
| 1 | 2 | 3 | 4 | 5 | 6 | 7 |
|
|
|
|
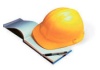 | Строительство |
| 1 | 2 | 3 | 4 | 5 | 6 |
|
|
|
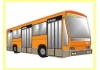 | Транспорт |
| 1 | 2 | 3 | 4 |
|
|
|
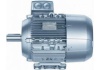 | Электротехника |
| 1 | 2 | 3 | 4 | 5 | 6 |
|
|
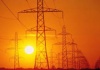 | Энергетика |
| 1 | 2 | 3 | 4 | 5 | 6 |
|
|
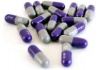 | Фармацевтика |
| 1 | 2 |
|
|
|
|
|
|
|
|
|
|
|
|
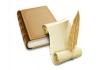 | Диссертации |
| 1 | 2 |
|
|